Claude Code x MCP x 3D CAD x 3D Printer
AI技術の進歩により、従来は専門的なCADスキルが必要だった3Dモデリング作業が、自然言語による指示で実現できる時代が到来しました。本記事では、Claude Code、MCP(Model Context Protocol)、Rhinoceros 3D、そして3Dプリンターを組み合わせて、自然言語の指示から椅子の3Dモデルを作成し、実際に物理的な椅子として出力するまでの一連のワークフローをご紹介します。準備したもの
Claude
Anthropic社が開発した大規模言語モデルを利用し、自然言語での複雑な指示を理解し、MCP(下記参照)経由にて適切なCAD操作コマンドに変換する役割を担います。
MCP(Model Context Protocol)
AI モデルと外部ツールを連携させるプロトコル。Claude CodeがRhinocerosを直接操作するためのブリッジとして機能します。
Rhinoceros 3D
業界標準の3D CADソフトウェア。精密な3Dモデリングが可能で、複雑な形状も効率的に作成できます。
3Dプリンター
デジタルモデルを物理的なオブジェクトとして出力するデバイス。
実装手順
ステップ1: 環境設定
- MCPサーバーの設定
- Rhinoceros用のMCPサーバーを構築
- ClaudeとRhinocerosの通信環境を確立
- Rhinocerosの準備
- 必要なプラグインのインストール
- MCP接続の確認
ステップ2: 自然言語による椅子デザインの指示
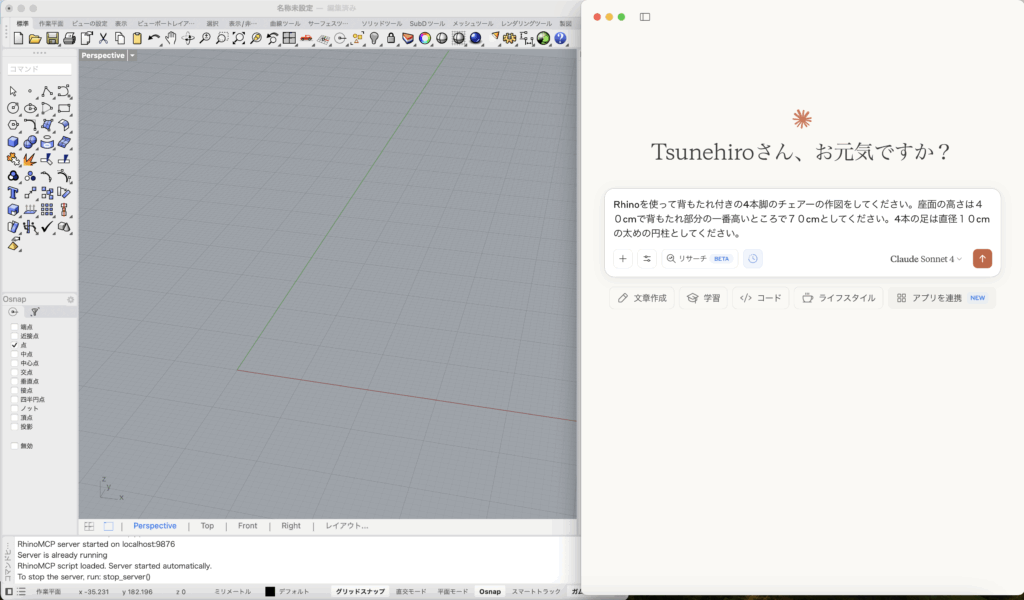
<左側がRhinoceros, 右側がClaude + MCP>
Claude AIに対して以下のような自然言語で椅子のデザインを指示:
「背もたれ付きの4本脚の椅子を作成してください。
- 座面は高さ40cm
- 背もたれは高さ70cm
- 脚部は4本脚で、直径10cm
- 太めの円柱形状の脚としてください。
ステップ3: Rhinocerosでの自動モデリング
Claude AIから設計指針に関する問い合わせがあり適宜対応し、作業を進める:
- 基本形状の作成
- 座面のベースとなる矩形の作成
- 適切な寸法での配置
- 座面の詳細設計
- 人間工学に基づいた座り心地を考慮した形状調整
- エッジの丸め処理
- 背もたれの設計
- 背骨の自然なカーブに沿った形状生成
- 座面との適切な接続部の作成
- 脚部の設計
- 安定性を考慮した脚の配置
- デザイン性と機能性のバランス調整
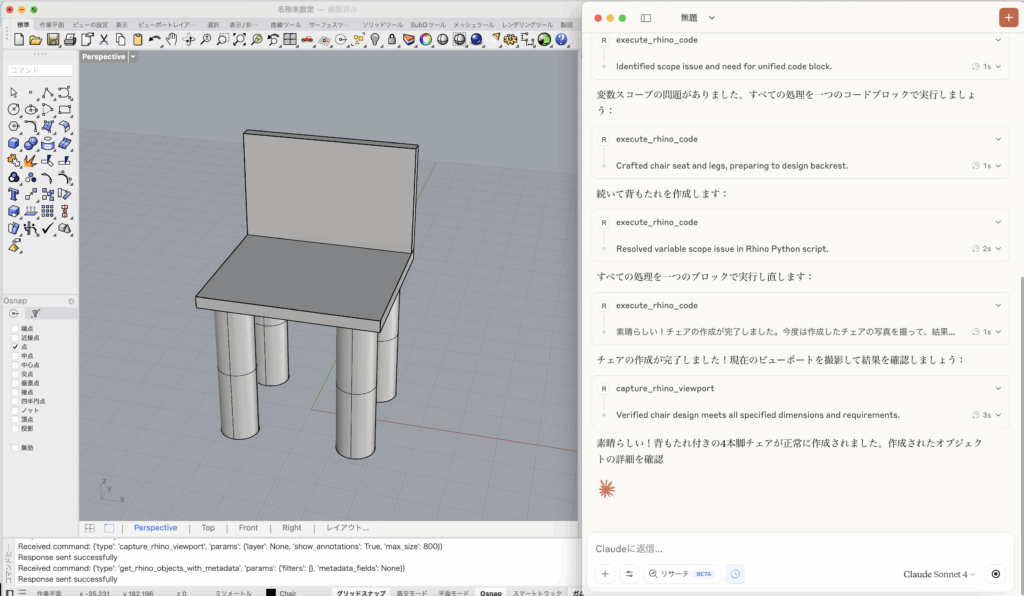
<一度もCADに触れる事なく、3Dモデルが完成>
ステップ4: 3Dプリント用データの準備
- メッシュ化
- Rhinocerosで作成したNURBSサーフェスをメッシュに変換
- 3Dプリンターに適した解像度での出力
- STLファイルの生成
- 3Dプリンター用の標準フォーマットでエクスポート
- プリントヘッドの動きを最適化
- スライシング設定
- レイヤー高さ、充填率、サポート材の設定
- プリント時間と品質のバランス調整
ステップ5: 3Dプリンターでの出力
- プリント準備
- プリンターのキャリブレーション
- 材料(PLA/ABS等)の準備
- プリント実行
- 設定に基づいた自動プリント
- 途中経過のモニタリング
- 後処理
- サポート材の除去
- 表面の仕上げ処理
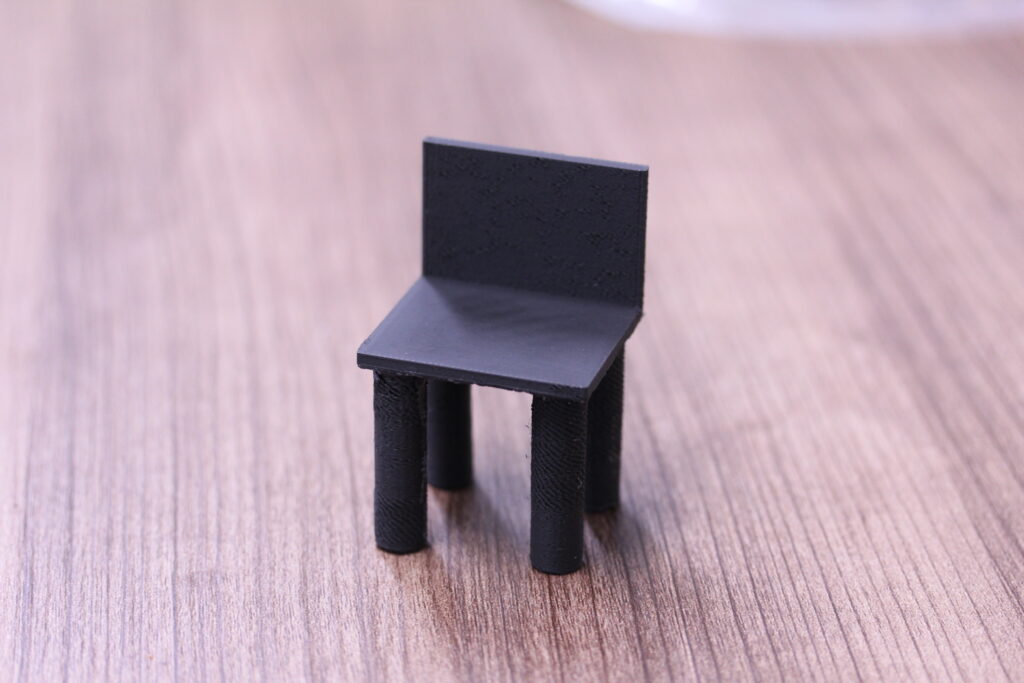
ワークフローの利点
1. 敷居の低下
従来はCAD操作の専門知識が必要だった3Dモデリングが、自然言語での指示により誰でも実行可能になりました。
2. 設計の効率化
複雑な形状も言葉で表現するだけで、AIが適切なCAD操作に変換して実行するため、設計時間が大幅に短縮されます。
3. 反復改良の容易さ
「背もたれをもう少し低くして」「脚をより細くして」といった修正指示も自然言語で行えるため、デザインの反復改良が簡単です。
4. 創作の民主化
専門的なCADスキルがなくても、アイデアを形にできるため、より多くの人が3D創作に参加できます。
技術的な課題と今後の展望
現在の課題
- 精度の限界: MCP経由にて使用出来るCADコマンドの制限などから、あまり複雑な形状には未対応
- 設計制約: 強度面・耐久面を考慮した形状や材料選定など、実運用に向けては強度・コスト等の配慮が必要
今後の発展可能性
- マルチモーダル対応: 与えられた2D画像から3Dモデルを推論しモデリングを行う(精度は低いが既に実装可能)
- 材料の多様化: 金属、セラミックなど多様な3Dプリンター材料次第で高強度な製品開発が可能
- 最適な製品設計: 機能面での必要条件を提示する事で、制約条件下での最適設計が可能
まとめ
Claude AI、MCP、Rhinoceros、3Dプリンターを組み合わせたワークフローにより、自然言語による指示から実際の物理オブジェクトまでの一貫した製造プロセスが実現できました。この技術は製造業、教育、個人創作など様々な分野での応用が期待されます。
特に注目すべきは、専門知識の壁を取り払い、アイデアを直接形にできる点です。今後、この技術がさらに発展することで、誰もがデザイナーや製造者になれる時代が到来するかもしれません。